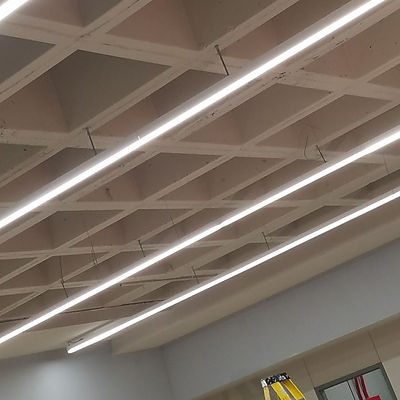
IRVING MIDDLE SCHOOL
As the San Antonio Independent School District (SAISD) continues to evolve and provide the highest quality educational experience for K -12 students, it has begun transforming some of its original middle school campuses into dual language academies. While the facility itself is being adapted for this highly demanded curriculum, the school has held long ties to the language arts. Irving Academy is named after the 19th century American author, Washington Irving, whose most famous works included “The Legend of Sleepy Hollow”, the short story “Rip Van Winkle” and was also known for dubbing New York City as Gotham. In a diverse community such as San Antonio, it was imperative for the SAISD to build capacity to develop English and Spanish curriculum with the goal of developing higher cognitive levels for students. Included in the 2016 Bond Program, the District identified the need to upgrade and replace the main electrical distribution system at the Irving Middle School campus. As Irving is now becoming a Pre-K though 8th grade dual language academy, special consideration for early childhood and elementary needs were factored into the vision and requirements for the design. To implement this vision, creative solutions were developed by the architectural and engineering team of O’Connell Robertson for the renovation of the existing 143,000 square foot Irving Middle School campus into an inspiring educational environment for English and Spanish learners. To provide further decades of service to the community, the engineering team designed a complete overhaul and modernization of the building’s MEP systems, including permanent stormwater controls, energy efficient HVAC systems, and low-flow plumbing fixtures.
Since the project required a multi-phased construction approach, there was close collaboration with the District to develop a plan for construction while the campus was occupied. During construction, the COVID-19 pandemic began and required the project team to keep construction on schedule with newly realized site restrictions. Despite these challenges, the team was able to leverage the time that students and teachers transitioned to virtual learning to expedite construction.
SAISD selected Bartlett Cocke to serve and Construction Manager for the project and Central Electric was selected to perform its electrical construction services including all major electrical systems, fire alarm, lighting controls and electrical gear distribution upgrades. Central Electric performed over 27,000 hours of work for the project. All work was performed with our own manpower and project partnerships included a variety of local vendors that provided “on-time” material distribution, routine safety inspections and jobsite audits, and specialty rental equipment.
All aspects of the work required extensive planning and coordination with the owner given the school’s busy schedule. The Central Electric team developed creative processes for installing the system while trying to maintain the existing system in other parts of the building. Additionally, our team had to closely engineer a system that attempted to follow the boundaries of the various construction phases, which required work in occupied and unoccupied areas. Pre-fabrication and quality control were a key component in dealing with these life safety systems. The new lighting control system was equally as complicated given the electrical circuiting for the corridor and egress emergency lighting did not necessarily follow the path of phased construction boundaries. Our team had to be creative of keeping existing lighting circuits energized while modifying and installing the new control system. As new remodeled areas were brought online, so were the new energy efficient lighting controls and emergency lights. Our team successfully deployed pre-fabricated components to speed the process and cut back on field labor.
Central Electric’s Project Manager reviewed the project plan drawings and specifications, including specialized building and construction requirements to ensure compliance with all aspects of the installation in sensitive work areas. This review included the identification of special equipment for handling and rigging switchgear, establishing procedures for receiving material deliveries and scheduling electrical outages. To meet the aggressive completion milestones, Central Electric developed its pre-fabrication and delivery schedule to reduce on-site installation time to the greatest extent possible. The plan required extensive coordination between trades and divisions of work to ensure sequencing and scheduling for installation and pre-fabrication of installed components. Central Electric’s approach for the project includes adherence to strict Safety Policies at the corporate/organizational level down to the specific project level job hazard analysis and measures to ensure safety for all aspects of work performed.
Through Central Electric’s dedication to incorporate project management best practices in its approach, it was able to complete the project with zero safety incidents, no added days for the project’s duration and on budget. Furthermore, the newly improved Irving Middle School facility will continue to serve students in San Antonio for decades to come.
​
Electrical Scope of Work
Central Electric was subcontracted by Bartlett Cocke General Contractors to provide its electrical construction services including:
​
-
Mobilization
-
Branch Conduit and Boxes
-
Branch Wiring
-
Feeder Conduit
-
Feeder Wiring
-
Distribution/Gear Installation
-
Fixture Installation and Trim Out
-
Low Voltage Rough-In
-
Gear Distribution Package
-
Light Fixture Package
​
Due to the project’s location in an active school campus, the Project Team was required to complete the work as quick as possible through carefully planned out phasing plans, as well as taking advantage of the school’s virtual learning and summer break. Additionally, the Project Manager kept in constant communication with the facilities management staff to phase work to avoid disruption of maintenance activities at the school. Central Electric sought to avoid any potential delays by performing two and three week “look ahead” planning which consisted of analyzing the project scope’s Work Breakdown Structure, extensive pre-construction planning to identify critical paths, workflows, resource allocations, risks, accounting of lead time for sourced components. Another critical aspect of the project consisted of the material handling process for hundreds of fixtures as well as thousands of feet of conduit and wiring. The magnitude of the project required extensive coordination with the vendors for “just in time” delivery and the school’s facility management staff for loading/unloading of materials.
​
An example of an innovative Project Management approach included the use of specialized equipment and software technology such as Plan Grid, Blue Beam and Site Docs. Central Electric leveraged technology to assist with daily online reporting, which was distributed to the Project Team highlighting project issues and communication of critical information. Central Electric was also able to create a link for the client to evaluate progress and real-time completion of tasks as they occurred. The use of technology provided greater awareness of project issues between all parties.
From a site safety perspective, Site Docs was used for weekly Toolbox Talks meetings and to collaborate with the General Contractor regarding awareness of safety requirements and specific job hazard analysis. Through Central Electric’s dedication to incorporating project management best practices in its approach, it was able to complete the project with zero safety incidents, no added days for the project’s duration and on budget.